Cruzer
Well-Known Hunter
Hey guys and gals. I had some extra time, so I thought I would take the time to document and share the technique I use to cut out a visor from a welding shield for installation. I'm using one of my CW Deathwatch fiberglass helmets, but it's pretty much the same on any fiberglass helmet. This might be common practice with all of the experience around here, but I thought I'd post something just in case or for the new members.
Take it easy,
Cruzer
First I cut channels on each side of the helmet with this bit. Once the channels are cut, I usually go back over the channels with some 120 grit or so sandpaper to smooth out the channels...
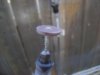
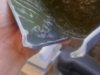
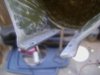
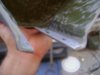
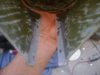
Next, I measure the width I'll need for the visor area on the helmet (I add 1/4" to each side to account for the channel). I apply blue painters tape (cleaner release) to the front of the welding visor, find the center line, trace the cut out visor area on the tape, and start marking for a symetrical visor. I usually leave about a 1/2" lip around the traced shape...
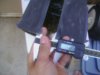
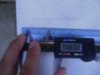
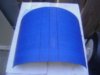
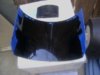
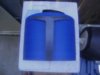
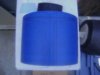
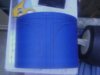
Then I start cutting out the visor with a cut off wheel and the Dremel set at a low RPM speed that almost seems like it will stop if pressed too hard. A higher setting melts the visor material quickly and creates more burrs. I make an initial channel with a first pass and then finish up and cut through with a second pass. I then carefully sand off the burrs with some 120 grit...
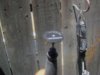
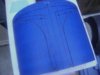
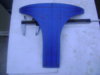
Now I have a perfectly fitted visor that is ready for glue-in installation, or I can drill out some holes for a removable visor installation using t-nuts, bolts, and acorn nuts...but that's a different tutorial!
Enjoy
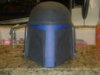
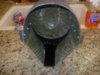

Take it easy,
Cruzer
First I cut channels on each side of the helmet with this bit. Once the channels are cut, I usually go back over the channels with some 120 grit or so sandpaper to smooth out the channels...
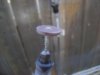
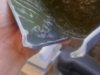
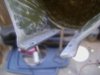
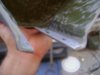
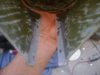
Next, I measure the width I'll need for the visor area on the helmet (I add 1/4" to each side to account for the channel). I apply blue painters tape (cleaner release) to the front of the welding visor, find the center line, trace the cut out visor area on the tape, and start marking for a symetrical visor. I usually leave about a 1/2" lip around the traced shape...
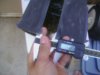
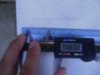
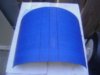
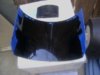
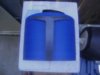
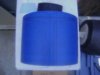
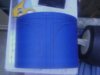
Then I start cutting out the visor with a cut off wheel and the Dremel set at a low RPM speed that almost seems like it will stop if pressed too hard. A higher setting melts the visor material quickly and creates more burrs. I make an initial channel with a first pass and then finish up and cut through with a second pass. I then carefully sand off the burrs with some 120 grit...
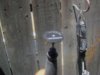
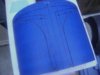
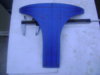
Now I have a perfectly fitted visor that is ready for glue-in installation, or I can drill out some holes for a removable visor installation using t-nuts, bolts, and acorn nuts...but that's a different tutorial!

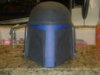
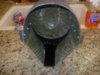

Last edited by a moderator: